Understanding Tube Fittings Dimensions
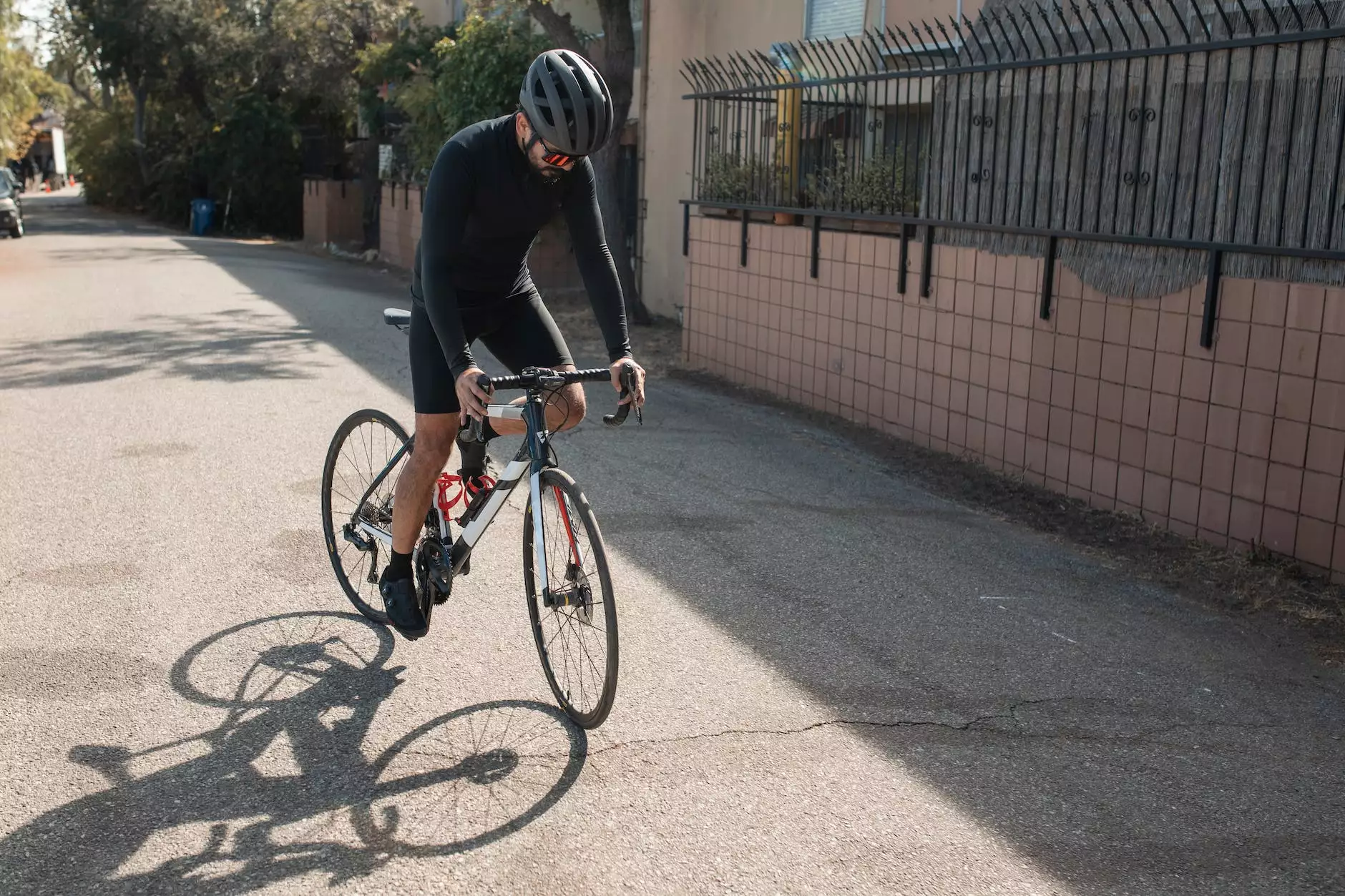
In the world of industrial piping and fluid management, tube fittings dimensions play a crucial role in ensuring effective and secure connections. Accurate fittings are vital for maintaining the integrity of systems in various applications, from water supply to hydraulic machinery. This article delves into the specifics of tube fittings dimensions, enlightening readers on their significance, types, and applications.
What Are Tube Fittings?
Tube fittings are mechanical devices that attach to the ends of valves, pipes, and tubes to form a tight seal, allowing for fluid transfer without leaks. They ensure that pipes are securely connected, preventing spills and potential hazards. High-quality tube fittings can withstand high pressure and temperatures, making them essential for many industries including oil & gas, chemicals, and pharmaceuticals.
Key Types of Tube Fittings
There are several types of tube fittings, each designed for specific applications and conditions. Understanding these differences is essential when discussing tube fittings dimensions.
1. Single Ferrule Tube Fittings
Single ferrule fittings utilize a single ferrule to secure the tube connection. They are relatively easy to install and widely used in low-pressure applications.
2. Double Ferrule Tube Fittings
Double ferrule fittings offer a more secure connection by using two ferrules. This design is suitable for high-pressure and critical applications, providing enhanced leak resistance and reliability.
3. NPT Fittings
National Pipe Thread (NPT) fittings are tapered thread fittings that create a seal by tightening threads. They are versatile and used in various plumbing and mechanical applications.
4. Other Variants
- Forged Pipe Fittings: Strong and durable, ideal for high-pressure systems.
- Threaded Pipe Fittings: Simple to install, commonly used in plumbing applications.
- Flanges: Used to connect pipes or valves, allowing for easy disassembly.
- Check Valves: Allow fluid to flow in one direction, preventing backflow.
- Ball Valves: Excellent for shut-off applications, providing quick and secure sealing.
- Needle Valves: Used for precise flow control.
- Manifold Valves: Often used to connect multiple pipes or tubes.
The Importance of Accurate Tube Fittings Dimensions
Understanding tube fittings dimensions is critical for several reasons:
- Safety: Ensures that connections won’t leak under pressure, preventing accidents.
- Efficiency: Proper fittings enhance the flow of liquids and gases, improving overall system performance.
- Cost-effective Solutions: Reducing leaks and failures minimizes downtime and maintenance costs.
- Compatibility: Ensures that all installed components fit properly, which is crucial in complex systems.
Key Dimensions to Consider in Tube Fittings
When choosing tube fittings, it's essential to be aware of the following critical dimensions:
1. Outer Diameter (OD)
The outer diameter is a vital measurement as it determines the size of the fitting and the compatibility with connecting tubes. Common outer diameters include sizes such as 1/4", 1/2", and 3/4". This dimension must be matched closely to ensure a snug connection.
2. Inner Diameter (ID)
The inner diameter indicates the space available for fluid flow within the tube. The ID should be as wide as possible, while still being compatible with other components and providing the necessary pressure ratings.
3. Wall Thickness
This measurement affects the strength and pressure rating of the fittings. Thicker walls may provide better resistance to high pressure and corrosion but can add weight to the system.
4. Length and Thread Pitch
For threaded fittings, the length of the thread and the pitch are crucial. The thread pitch must match the companion fitting to ensure a proper seal. These dimensions can vary widely based on the fitting type.
Materials Used in Tube Fittings and Their Impact on Dimensions
The material used to manufacture tube fittings influences their dimensions and performance characteristics. Here are some common materials:
1. Stainless Steel
Stainless steel fittings are resilient and resistant to corrosion. They often have tighter tolerances, making them suitable for a wide range of applications, particularly in food and pharmaceutical industries.
2. Brass
Brass fittings are well-known for their durability and corrosion resistance. They are often used in low-pressure systems and offer good machinability.
3. Plastic
Plastic fittings are lightweight and resistant to chemical corrosion. However, they may not handle high pressure as effectively as metal fittings.
Applications of Tube Fittings in Various Industries
Tube fittings have diverse applications, making them indispensable in multiple industries.
1. Oil and Gas Industry
In this industry, tube fittings are vital for maintaining secure connections in high-pressure environments, whether in offshore drilling or refining processes.
2. Chemical Processing
Corrosion-resistant fittings are crucial for transporting aggressive chemicals. The right dimensions help prevent leaks, ensuring safety and compliance with regulations.
3. Pharmaceuticals
In pharmaceuticals, tube fittings must meet strict standards to prevent contamination. Stainless steel fittings with precise dimensions are typically preferred.
4. Food and Beverage
Food-grade fittings ensure that food products remain uncontaminated. These fittings must comply with health and safety regulations, maintaining structural integrity during production processes.
Choosing the Right Tube Fittings for Your Application
When selecting appropriate tube fittings, consider the following steps:
- Identify Requirements: Determine the precise pressures, temperatures, and fluid types involved.
- Review Specifications: Compare materials and dimensions to ensure compatibility with existing systems.
- Consult Experts: If unsure, consulting with industry professionals can provide valuable insights.
- Quality and Standards: Verify that the fittings meet relevant industry standards to ensure safety and reliability.
Conclusion
In summary, understanding tube fittings dimensions is essential for anyone involved in fluid management or engineering. The right dimensions impact safe, efficient, and reliable systems across numerous industries. Whether dealing with hydraulic systems, chemical processing, or plumbing, utilizing the correct tube fittings is a fundamental aspect of maintaining operational integrity. For more information on various tube fittings and their dimensions, visit TechTubes.in, your trusted resource for all tube fitting needs.