The Importance of **LEV Testing** in **South Wales**
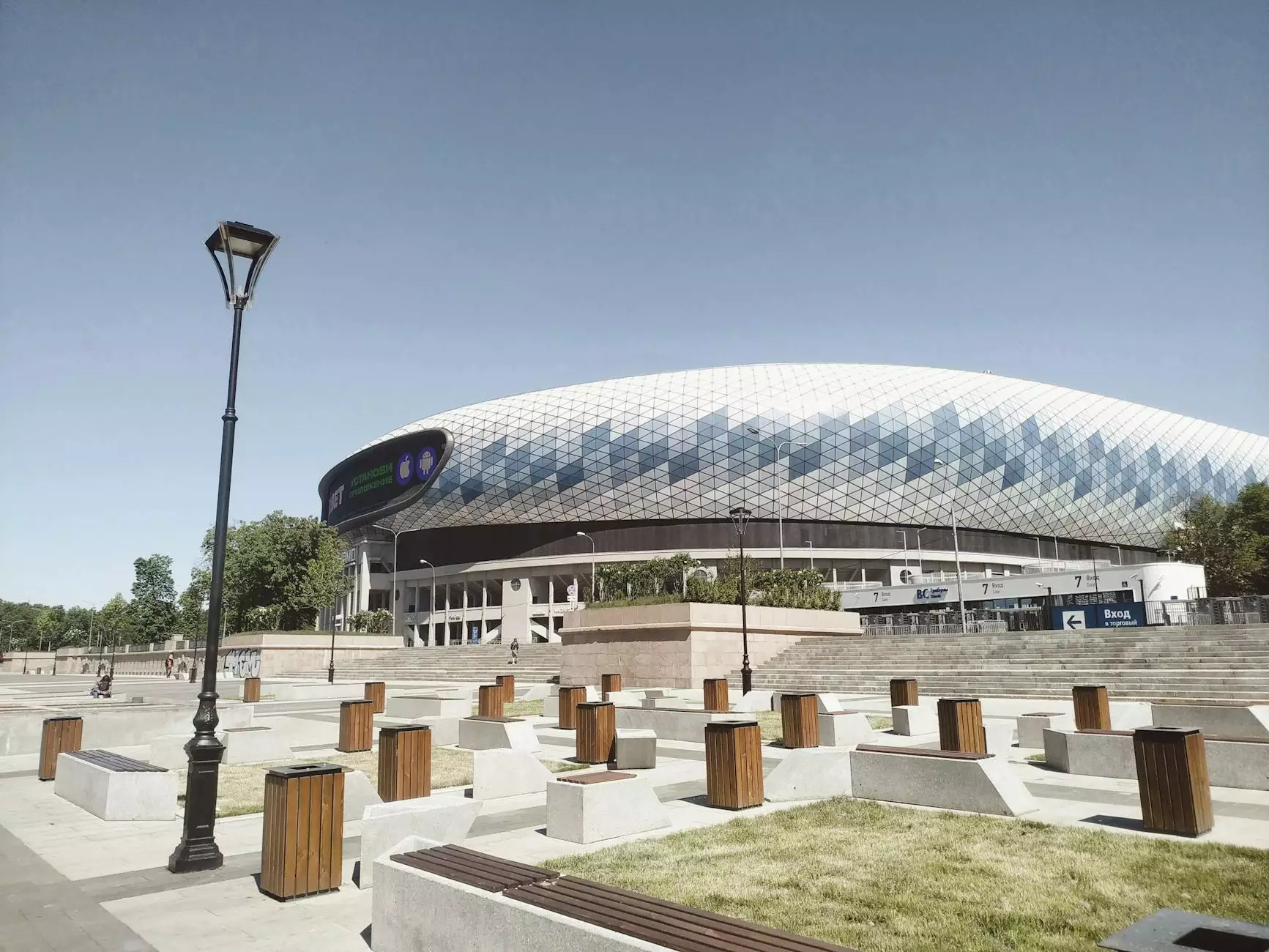
In an ever-evolving industrial landscape, ensuring a safe working environment is paramount. One essential aspect of maintaining workplace safety is through Local Exhaust Ventilation (LEV) testing, an indispensable process for businesses across South Wales. This article will delve deep into the significance of LEV testing, exploring its benefits, legal obligations, and best practices to help organizations maintain compliance and ensure safety.
What is LEV Testing?
LEV testing involves the examination of ventilation systems designed to capture and remove harmful airborne contaminants generated during various industrial processes. These contaminants can include dust, fumes, and vapors that pose significant risks to workers' health and safety. Ensuring your LEV system is functioning effectively is crucial for:
- Protecting the health of your employees
- Reducing the risk of occupational illnesses
- Complying with health and safety regulations
- Improving operational efficiency
Why is LEV Testing Essential for Businesses in South Wales?
LEV testing is not merely a regulatory requirement; it is a crucial component of workplace safety management. Here, we outline several reasons why your business in South Wales should prioritize this testing.
1. Legal Compliance
In the UK, various health and safety regulations mandate the need for routine LEV testing. The Control of Substances Hazardous to Health (COSHH) Regulations require employers to ensure that effective control measures are in place to minimize exposure to hazardous substances. Regularly conducting LEV tests helps businesses remain compliant, avoiding potential legal issues and penalties.
2. Protecting Employee Health
Ensuring the health and safety of your workforce should always be a top priority. LEV testing plays a vital role in protecting employees from health risks associated with airborne contaminants. By effectively removing harmful substances, you reduce the chance of respiratory illnesses, skin problems, and other occupational hazards. A healthier workforce often translates to increased productivity, fewer sick days, and a better overall workplace atmosphere.
3. Enhancing Operational Efficiency
Effective ventilation systems not only safeguard health but also enhance operational efficiency. When your LEV systems are functioning optimally, they help to:
- Improve air quality, leading to better employee morale and productivity
- Increase machinery lifespan by minimizing dust and chemical residue buildup
- Reduce downtime caused by health-related issues
4. Demonstrating Corporate Responsibility
Today's consumers and clients are increasingly conscientious about corporate responsibility. By prioritizing LEV testing and demonstrating a commitment to employee safety and well-being, your business enhances its reputation. This commitment can lead to increased customer loyalty and improved brand perception in the market.
Key Components of LEV Testing
A comprehensive LEV testing process includes several critical components. Understanding these elements can help businesses better prepare for assessments and ensure their systems are effective.
1. Thorough Inspection of Systems
This initial phase involves a detailed inspection of the ventilation systems in place. Key areas of focus include:
- Fan performance and airflow
- Ductwork integrity
- Capture zones and hoods
- Filters and their conditions
2. Airflow Measurements
Accurate airflow measurements are crucial in determining whether an LEV system effectively captures contaminants. This process involves using specialized tools to assess:
- Velocity of airflow at various points
- Pressure differentials across components
3. Performance Assessment
The overall performance of the LEV system is evaluated against established benchmarks. This may include comparing measurements to manufacturer specifications and regulatory requirements.
4. Documentation and Reporting
After conducting the tests, a detailed report is generated. This report typically includes:
- Overview of the LEV systems tested
- Results of airflow measurements
- Photographic evidence of conditions
- Recommendations for improvements or necessary repairs
How Often Should LEV Testing Be Conducted?
Determining the frequency of LEV testing can depend on various factors, including the type of operations, the level of contaminants present, and specific regulatory requirements. However, a general recommendation is to conduct LEV testing at least once a year and more frequently in high-risk environments. Continuous monitoring helps ensure that your systems remain effective over time.
Choosing the Right LEV Testing Provider in South Wales
As a business owner, selecting an experienced and reputable LEV testing provider is essential for ensuring compliance and safety. Here are some tips to consider when choosing a service:
- Industry Experience: Look for providers with extensive experience in your industry. They will better understand your specific needs and regulatory requirements.
- Accreditations: Ensure the provider is accredited and follows guideline protocols recognized by regulatory bodies.
- Comprehensive Services: Choose a provider that offers a full range of services, including assessments, reporting, and recommendations for improvements.
- Customer Reviews: Research testimonials and reviews from previous customers to gauge the provider’s quality of service.
Case Studies: Successful LEV Testing Implementation
To illustrate the effectiveness of proper LEV testing implementation, let’s explore a few case studies of businesses in South Wales that have successfully navigated this process.
Case Study 1: Manufacturing Plant
A local manufacturing plant faced challenges with dust accumulation affecting employee health and machine performance. Upon conducting LEV testing, it was discovered that their systems were not adequately capturing fine particulate matter.
Following the recommendations provided in the LEV report, the company invested in updated hood designs and improved filter systems. Within months, they witnessed:
- A 40% reduction in reported respiratory issues among employees
- Increased machinery efficiency and lifespan
- An overall boost in workplace morale
Case Study 2: Chemical Processing Facility
Another example involves a chemical processing facility where employees frequently worked with hazardous substances. Regularly scheduled LEV testing revealed that the existing systems were outdated and failing to meet safety standards.
The facility took proactive steps to upgrade their systems based on the assessment results. Post-implementation, the facility noted:
- Improved compliance with health and safety regulations
- A significant decrease in incidents related to hazardous exposure
- A positive shift in company culture, emphasizing safety and well-being
Conclusion: Prioritizing LEV Testing for a Safer Future
In summary, LEV testing is a critical component of workplace safety in South Wales. By prioritizing this essential practice, businesses can protect the health of their employees, enhance operational efficiency, and demonstrate corporate responsibility.
At SafePlant UK, we specialize in providing comprehensive LEV testing solutions tailored to your business’s unique needs. Ensuring your workplace is safe and compliant is not only a legal obligation but a moral imperative. Investing in quality LEV systems and regular testing can lead to a healthier workforce, improved productivity, and ultimately, a more prosperous business.
Contact us today to learn more about our services and how we can assist you in achieving your safety and compliance goals.
lev testing south wales