The Importance of Auto Molds in the Metal Fabrication Industry
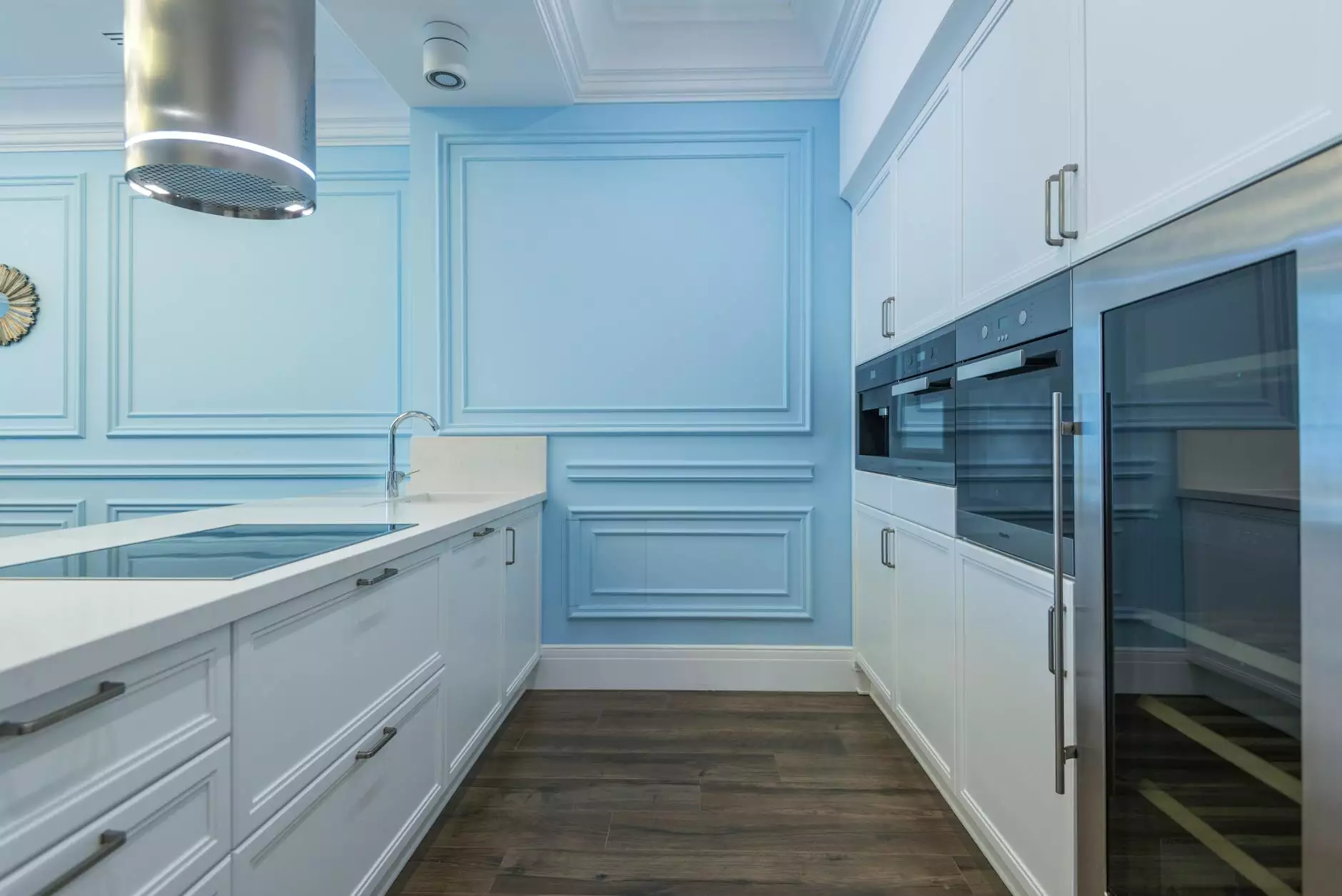
In today's rapidly evolving manufacturing landscape, auto molds play a pivotal role in optimizing production processes and ensuring the quality of end products. The area of metal fabrication stands to benefit greatly from the precision and reliability provided by advanced mold technology. As industries push towards higher efficiency and lower costs, understanding the fundamental aspects of auto molds becomes vital for businesses aiming to stay competitive.
1. What Are Auto Molds?
Auto molds are specially designed tools or forms used in the manufacturing process to shape materials—typically metals or plastics—into desired configurations. These molds are essential in creating consistent and high-quality parts for various applications. In the automotive sector, auto molds are used to produce components such as body panels, frames, and other intricate parts that require a high degree of precision.
2. The Role of Auto Molds in Metal Fabrication
Metal fabrication encompasses a range of processes that involve cutting, bending, and assembling metal structures. With the integration of auto molds, the entire process is enhanced, leading to:
- Increased Efficiency: Automated processes enable quicker production timelines, reducing the time from concept to completed product.
- Cost-Effectiveness: High-quality molds reduce waste and ensure precision, which leads to cost savings in both materials and labor.
- Consistency: Molds ensure that every part produced meets the same specifications, enhancing the overall quality of products.
- Customization: Innovative molding techniques allow for the production of customized components that meet specific client requirements.
3. Types of Auto Molds
Within the realm of auto molds, several types exist, each tailored to different manufacturing needs. They include:
- Injection Molds: Commonly used for producing plastic parts, these molds inject molten material into a cavity where it cools and solidifies.
- Blow Molds: Ideal for creating hollow plastic products, blow molds are used in producing containers like bottles.
- Compression Molds: Suitable for making thick or larger products, compression molds involve pressing material into a mold cavity and heating it to set the shape.
- Die Casting Molds: Primarily used for metals, die casting molds allow for the production of complex shapes by forcing molten metal into the mold.
4. The Technological Advancements in Auto Molds
The manufacturing industry has witnessed enormous technological growth, greatly benefiting the development and functionality of auto molds. Key advancements include:
- 3D Printing: Rapid prototyping through 3D printing technology allows manufacturers to create molds at a fraction of the time, leading to faster design iterations.
- Computer Numerical Control (CNC) Machining: CNC machines offer precision in mold making, enhancing the accuracy of details in the final products.
- Simulation Software: Software tools that simulate the molding process help identify potential issues before production begins, saving time and resources.
5. Choosing the Right Auto Mold Manufacturer
When selecting a manufacturer for auto molds, consider the following factors to ensure high-quality partnerships:
- Experience: Look for manufacturers with a proven track record in the industry and extensive knowledge of various molding techniques.
- Technology Proficiency: Ensure the manufacturer has access to the latest technology and equipment that can produce precise molds.
- Customization Capabilities: A reputable manufacturer should be able to tailor molds to meet unique specifications.
- Quality Assurance: Choose a company that emphasizes quality control and offers guarantees on their products.
6. The Impact of Auto Molds on Sustainability
Sustainability is crucial in the modern manufacturing landscape. Auto molds contribute significantly to sustainable practices through:
- Material Efficiency: Precision in mold design reduces material waste during production.
- Energy Reduction: Advanced molds can streamline the manufacturing process, requiring less energy overall.
- Recyclability: Many molds are designed to work with recyclable materials, ensuring that waste can be minimized.
7. Future Trends in Auto Molds
The future of auto molds is bright, with several exciting trends on the horizon:
- Smart Manufacturing: The integration of IoT (Internet of Things) in mold making will revolutionize tooling processes, allowing for real-time monitoring and adjustments.
- Advanced Materials: As material sciences advance, the development of new compounds could result in lighter, stronger molds capable of withstanding greater pressures.
- Increased Automation: Automating the production and maintenance of molds can further enhance efficiency and reduce downtime.
8. DeepMould: A Leader in Auto Molds
At DeepMould, we specialize in providing top-tier solutions for auto molds tailored to the needs of our clients in the metal fabrication industry. Our commitment to innovation, quality production, and customer satisfaction sets us apart. By leveraging the latest technologies and a highly skilled workforce, we ensure that our clients receive exceptional products that meet the highest industry standards.
Conclusion
In summary, auto molds are a fundamental element of modern manufacturing, particularly in the metal fabrication sector. Their role in improving efficiency, maintaining quality, and driving innovation cannot be overstated. As the industry continues to evolve, staying informed about the technologies and practices surrounding auto molds will be essential for businesses looking to thrive. Partnering with knowledgeable manufacturers like DeepMould will enhance your production capabilities and ensure consistent top-quality products.